Our commitment at BPS is to remove the barriers between great ideas and bringing them to market.”
MANUFACTURING AND PRODUCTION CAPABILITIES
Through a tailored process, we provide individualized services to our clients. We specialize in design consultation, sourcing research, pricing, planning & control production, QC and shipping.
BASIC INFO
To begin working on the price, we will need to receive the information listed above.
PRODUCT DEVELOPMENTThis includes all the little extras - brand labels, size/care labels, hang tags, buttons, zippers and more. Development can take 30-60 days depending on complexity and back and forth. We recommend having all trims approved by the time the PO is placed to avoid any delays. Also keep in mind minimums are high (in the thousands), so we recommend consolidating where possible.
Lead time: First protos in available yarn (2-3 weeks) Fit comments, corrections (1-2 weeks) Sales samples (60-120 days depending on yarn and quantity) Production (75, 90-120 days depending on yarn and quantity)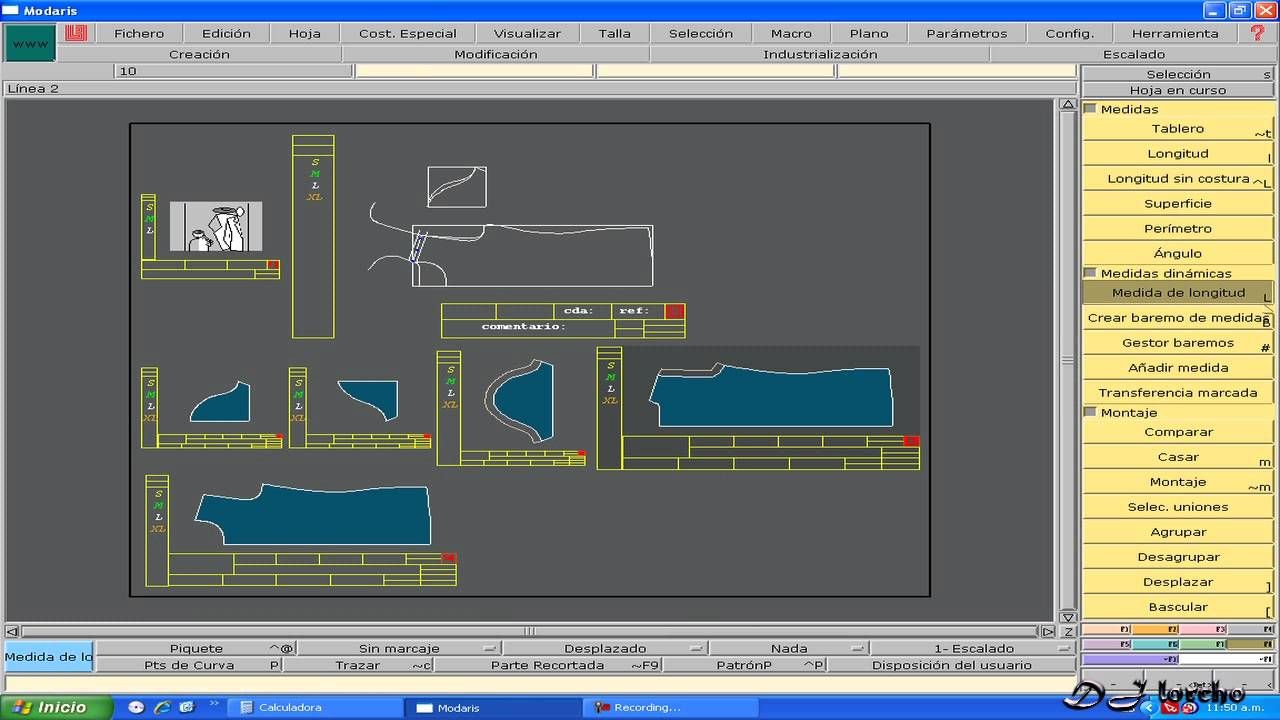
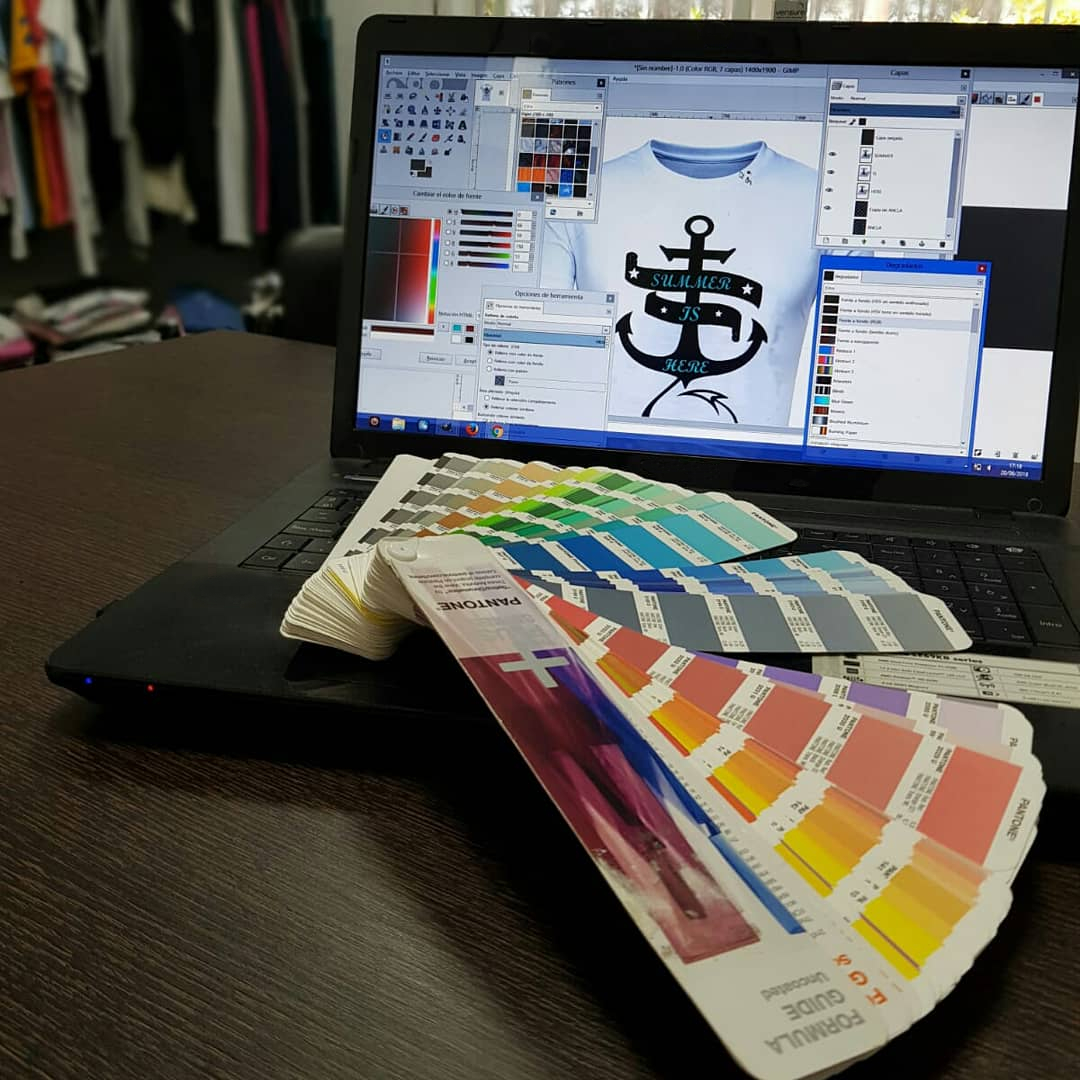
A big part of success in the manufacturing endeavor is finding the right fit. Different suppliers have different experiences and different strengths, so it is keys to find the one that can not only produce that you need, but be passionate about it. The design process is something that is fluid. However, if we have to make an entirely new sample we charge a new sampling fee. If the changes are on the existing sample we will do up to 2 revisions at the production price.
The Design and Product Development department is essential as we are focused in offering our customers a total support in fabric knitting, sewing construction and trims, which will allow us to get the expected result in the final product.
To get this, we count with a qualified people who assess, analyze and repose the correct path for each product, to ensure an optimal development process to be reflected later in our bulk production. In this way, we guarantee to accomplish the lead time offered and with the quality requested by our customers.
Quality is checked along the whole process. Once the garment is completed, it goes through an inspection process and then taken to the finish area. The quality control is the application of mechanism, actions and tools designed to detect mistakes.
Key controls
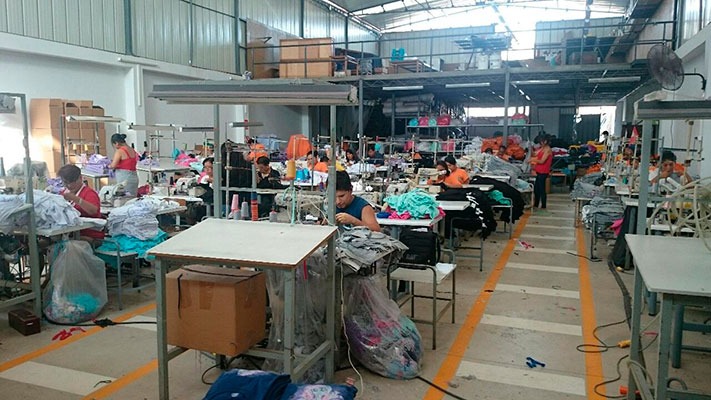
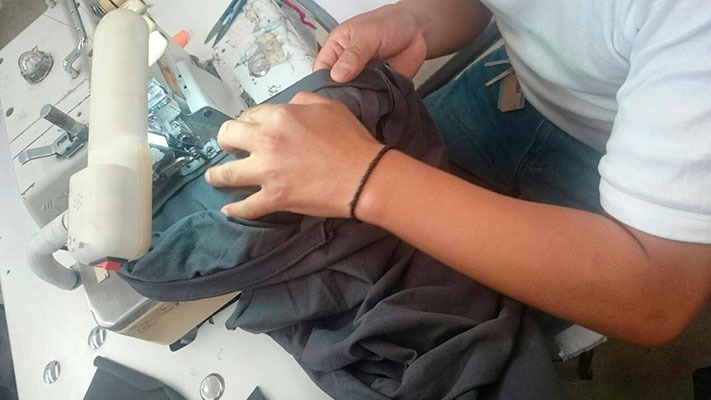
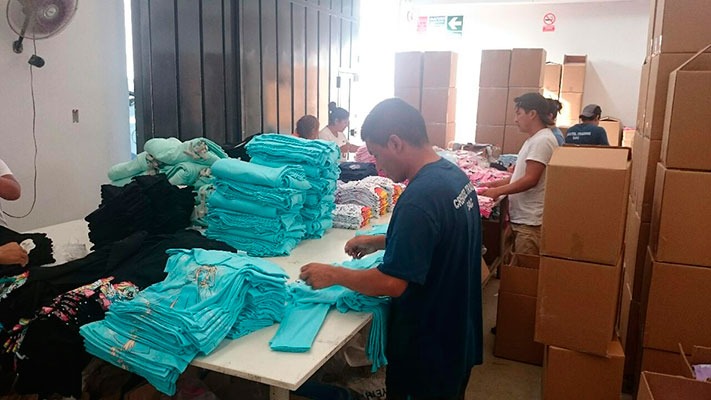
The finished garments are steamed, folded, put in a polybag and put in a carton. Finally, a random audit is conducted within our standard quality control process to ensure the quality of the product delivered. We will offer our standard procedure for packing, if the client wants something different, they must specify. If the packaging requirements are extensive/involved, additional fees may apply.
We ship anywhere in the world! We offer to our Customers the goods be placed in your business door, Warehouse or delivery address you would like to receive the goods. We coordinate with our Forwarder and make the flight reservation, Customs process in destination for the release, coordinate with the Trucker in destination for your final delivery (previous appointment)
If you would like to use this service, then you will need to specify at the moment we begin to work on the final pricing, this way we can give you a Landed Price for your product.
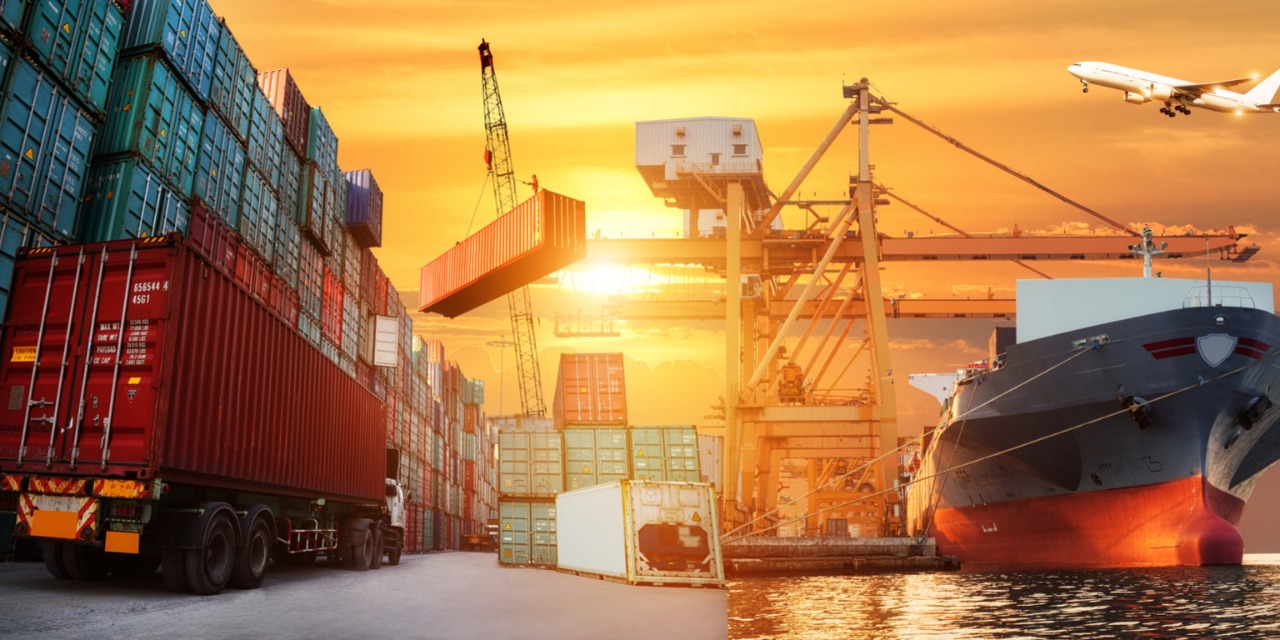
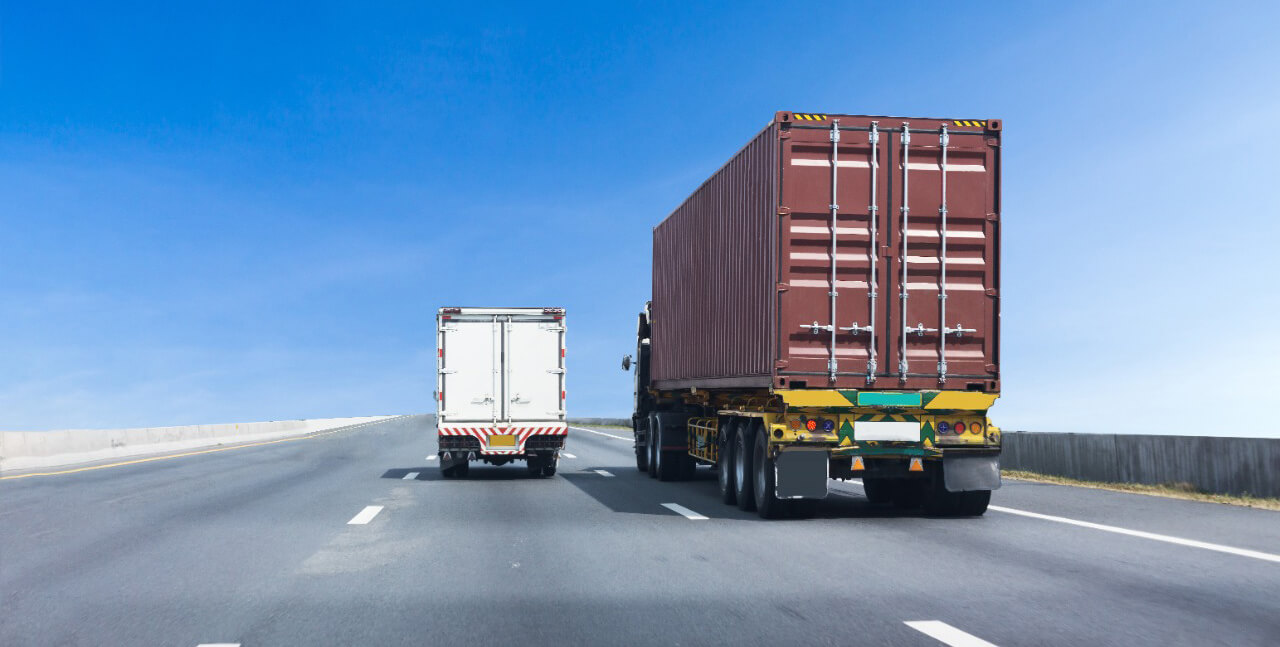
Interested in becoming a partner?
By removing every pain point and risk, we believe we can empower millions of people to launch their own products with the same quality and economies of scale as a major retail brand.